射出成形の不良「シルバーストリーク」「フローマーク」「ガス焼け」の発生原因と対策
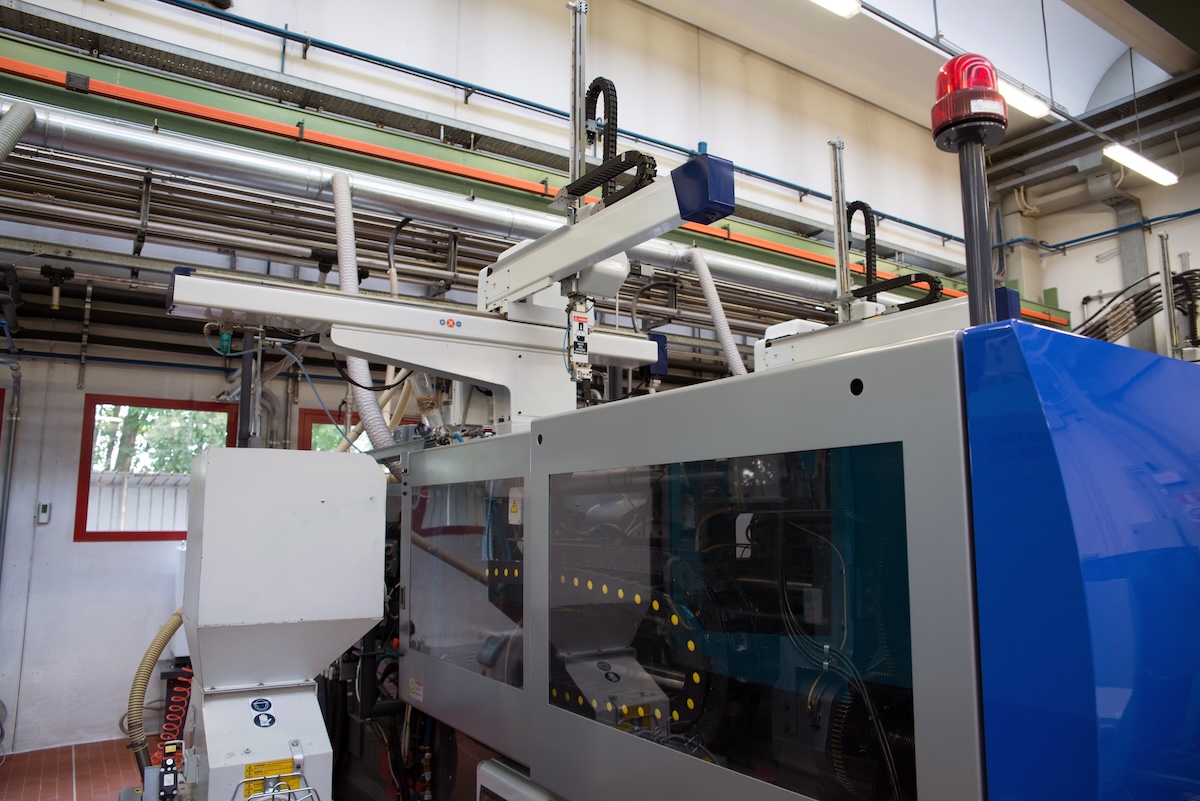
射出成形の製造工程において、製品の外観・性能に不具合が発生する「成形不良」の原因はさまざまで、不良の種類も多くあります。
この記事では、合成樹脂(プラスチック)製品設計の現場でよくあるトラブルをもとに、射出成形における代表的な成形不良「シルバーストリーク」「フローマーク」「ガス焼け」の原因と対策について解説していきます。
射出成形不良『シルバーストリーク』
射出成形不良『シルバーストリーク』とは?
シルバーストリークは、成形品の表面に樹脂が流れる方向に合わせて銀白状の筋が発生する現象です。
射出成形不良『シルバーストリーク』の障害
シルバーストリークは成形品の表面に現れてしまうため、外観不良となります。
PC、PBT、PET、LCPなどの加水分解しやすい樹脂を材料に使用している場合にシルバーストリークが発生している場合は、成形時に材料が加水分解して劣化していることを意味します。
一方、塗装や印刷を行う成形品では、塗装やインクの剥離の原因になります。
発生原因とその対策
シルバーストリークの発生メカニズム
射出成形時に樹脂の中で発生した気泡が金型内で引き伸ばされ、充填過程で潰れることで樹脂の表面に銀色の筋となって現れる
シルバーストリークの発生原因の多くは、材料である樹脂の乾燥不足です。乾燥が不十分な材料を使用して成形すると、樹脂内の水分が射出成形時の加熱によって水蒸気になり、シルバーストリークが発生しやすくなります。
成形機のシリンダー内の脱気不良(水分、揮発分等)やサックバック(保圧後や計量後に成形機のスクリューを後退させる動作)によるノズル部分でのエアー過多、ホッパー(射出成形機に材料を供給する漏斗状の装置)側からのエアーの巻き込み、ノズル合わせ面の腐食による樹脂滞留分解ガスの巻き込みなども原因となります。
また、金型の形状が適切でないと、射出成形時に発生したエアーを排出できず、樹脂の中で発生した気泡が引き延ばされてシルバーストリークが発生します。
シルバーストリークは以下の3段階で発生します。
①充填中の流動部分またはシリンダー中に気泡が発生する
②この気泡が押し出され、さらにキャビティー(金型の凹部)壁面に押し付けられる
③気泡が潰れてシルバーストリークになる
以下に、成形条件・金型・材料・形状ごとにシルバーストリークが発生する原因と代表的な対策をまとめました。
推定原因 | 代表的な対策 | |
---|---|---|
成形条件 |
|
|
|
|
|
|
|
|
|
|
|
|
|
|
金型 |
|
|
|
|
|
|
|
|
材料 |
|
|
|
|
|
|
|
|
形状 |
|
|
|
|
|
|
|
射出成形不良『フローマーク』
射出成形不良『フローマーク』とは?
フローマークは、製品の表面に溶融した樹脂が流れた跡が残ってしまう現象です。
成形品のコーナー部や凹凸部などに白雲状の模様が発生する場合と、ゲート(金型内の製品部に樹脂を充填するための入り口)から蛇行状の模様が発生する場合があります。
射出成形不良『フローマーク』の障害
外観不良になるだけではなく、強度の低下や反り、寸法バラつきの原因にもなります。
発生原因とその対策
フローマークの発生メカニズム
ゲート内で溶融樹脂が冷え、流動性が下がることで発生する
白雲状の模様は、固化した樹脂が流れる過程で引き伸ばされ、クレイジング(射出成形で成形品にできる細かいひび割れや欠けなどの表面欠陥)が出たり、屈折率の変化によって現れます。
蛇行状の模様は、最初に紐状になって流れた樹脂の表面がメルトフラクチャと言う肌荒れの現象を起こし、その状態で固まることで現れます。
ゲートから入った溶融樹脂は、通常はゲート側から徐々に充填されて末端に向かい流れ始めますが、図のように、まず紐状になった樹脂が先端に向かって流れ、その後ゲート側から充填が進行することが原因です。
以下に、成形条件・金型・材料・形状ごとにフローマークが発生する原因と代表的な対策をまとめました。
推定原因 | 代表的な対策 | |
---|---|---|
成形条件 |
|
|
|
|
|
|
|
|
|
|
|
|
|
|
金型 |
|
|
|
|
|
|
|
|
材料 |
|
|
|
|
|
|
|
|
形状 |
|
|
|
|
|
|
|
射出成形不良『ガス焼け』
射出成形不良『ガス焼け』とは
ガス焼けは、樹脂から発生したガスが、金型のガス抜けが悪い箇所や最終充填箇所で圧縮されて高温になることで、その周りの樹脂が黒く焼け焦げる現象です。
射出成形不良『ガス焼け』の障害
ガス焼けは目視で容易に判断できるため、外観不良となります。さらに、ガス焼けが発生しているということは、成形時に材料が劣化していることを意味する場合もあります。
発生原因とその対策
ガス焼けの発生メカニズム
金型内のガス抜けが悪い箇所にて、ガスが圧縮されて高温になることで、接する樹脂が黒く焼け焦げる
一般的な射出成形では、樹脂が充填する前の金型内に空気が存在しています。そこにゲートから樹脂を注入するのですが、材料を融解させた際に発生したガスや金型内の空気がどんどん逃げ場を失い圧縮されていきます。
最終的に、ガスベント等が不充分で逃げ切れなかったガスや空気はそのまま圧縮され、断熱圧縮により発火し、樹脂を黒く焦がして焼け跡が付いてしまいます。
自転車のタイヤに空気を入れる際、空気入れを激しく押し続けると空気入れが熱くなりますが、それと似たような現象が起きているといえます。
以下に、成形条件・金型・材料・形状ごとにガス焼けが発生する原因と代表的な対策をまとめました。
推定原因 | 代表的な対策 | |
---|---|---|
成形条件 |
|
|
|
|
|
|
|
|
|
|
|
|
|
|
金型 |
|
|
|
|
|
|
|
|
材料 |
|
|
|
|
|
|
|
|
形状 |
|
|
|
|
|
|
|
材料供給装置への乾燥エアー供給による「シルバーストリーク」の対策
射出成形で成形品の材料として使用される樹脂ペレットには、表面の水分付着や、樹脂内の吸湿性があります。
温度や湿度などに左右されやすいため、一般的に成形前の乾燥が必要ですが、適切に乾燥されていない、十分な乾燥がされていない、乾燥にバラつきがある、というような乾燥トラブルは、シルバーストリークなどの成形不良の原因となります。
樹脂成形の品質を向上させて不良率を改善するには、湿度・乾燥の徹底管理が重要です。日邦産業では材料特性に合わせて除湿乾燥機、真空乾燥機の使い分けを行います。また、材料タンクに乾燥エアーを流し込んで材料乾燥状態を安定させることで、射出成形品の品質安定と生産性の向上を目指しています。
日邦産業の強み〜工程内検査機による自動検査での成形不良対策〜
高感度のCCDカメラを用いて金型内の検査を行うことで、成形不良を検知することができます。また、不良発生箇所の推定には、金型キャビティ内での樹能充填過程をアニメーションで確認し、熱可塑性樹脂での充填解析を行う流動解析が効果的です。
金型内の検査と不良発生箇所の推定
日邦産業では、樹脂成形品を製造する過程で高感度のCCDカメラを利用して製品を撮影し、バリ・異物・接点・割れ・欠品等の自動検査を行います。
自動検査により成形不良の検出精度が向上し、成形不良を迅速かつ効率的に検知することでコストダウンが可能です。その他にも、射出成形における不良を高精度に検出するさまざまな技法を用いています。
1/1000mm(1ミクロン)単位で測定する三次元測定器を用いた品質検査を実施。製品の形状や寸法を高精度に測定していきます。
また、2D、3D、CADを使用し、データに基づいて金型の設計を見直すことで、成形不良を減らすことができます。
流動解析を利用した不良の見極めと対策
射出成形において、金型内の樹脂の流れは成形不良の発生に大きく影響します。
そこで、本来は見ることができない金型内の樹脂の流れを解析し、各種不良の発生予測と対策を行うため「流動解析」というツールが使用されます。
流動解析についてはこちらの記事でご紹介しています。
詳しくはこちら>>射出成形の不良「ヒケ」「ボイド」「バリ」の発生原因と対策
射出成形における不良にお困りの方や、成形品質の改善、生産性の向上をご希望の方は、製品の構想設計段階よりお手伝い出来る日邦産業にぜひご相談ください。
射出成形に関するお問い合わせ・試作のご依頼はこちら
日邦産業は、射出成形・成形材料・金型製作に関するお問い合わせを随時受け付けております。ご不明点や記事にはないお困りごとのあるお客様には、個々の状況に応じて最適なご提案をいたします。まずはお気軽にご相談ください。
日邦産業株式会社お問い合わせフォーム