射出成形に必要な金型を徹底解説!
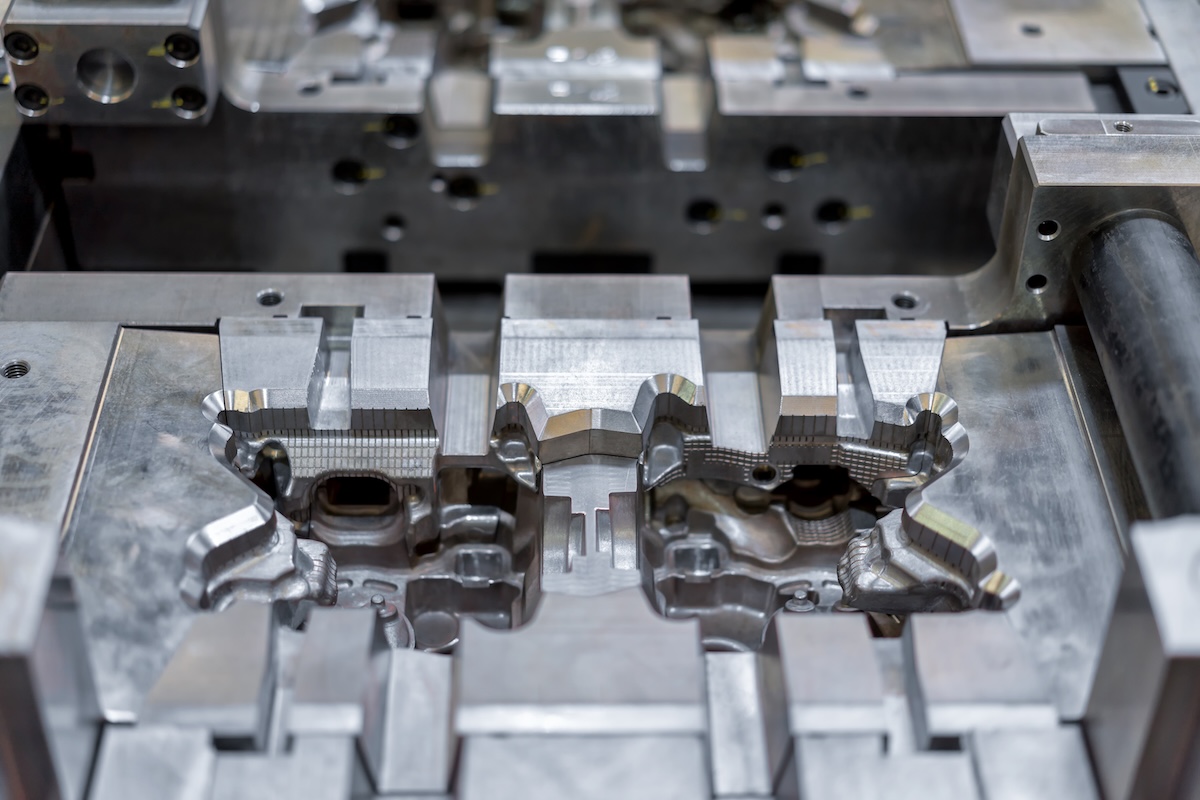
射出成形では、複雑な形状、様々なサイズの製品を製造するために「金型」を使用します。成形品の品質や生産性を左右する要素として、金型の良し悪しは製品の良否に直結するため、金型の設計は非常に重要です。
この記事では、射出成形に必要な金型の基本的な知識から製造に関する専門情報まで幅広くご紹介します。
金型とは
金型とは、金属や樹脂製の部品を塑性加工(被加工材に型を押しつけて目的とする形状をつくる方法)や成形などの加工方法に用いる、主に金属製のツールのことです。
射出成形においては、造りたい部品やパーツを模った金型の中に高温で熱して柔らかくなった樹脂を流し込んで冷却することで、樹脂製品を形造ることができます。日用品をはじめ、家電、自動車、航空宇宙分野などその用途は様々です。
プレス金型
射出成形金型
ブロー成形金型
押し出し成形金型
金型の最大のメリットは、一度金型を造ってしまえば大量生産ができることです。金型の設計や製作時に費用はかかりますが、その後は比較的低コストかつ短時間で同一製品を大量生産することが可能です。
金型を用いたプラスチック成形のメリット
1.高精度で大量生産が可能
生産数が少ない場合は、金型を作るよりも樹脂をそのまま削って作る切削加工や、シリコン型を用いて製造する注型の方が短時間で安くできます。しかし生産数が多くなると、特に切削加工は精度にばらつきが出ること、加工に時間がかかるためコストメリットがありません。精度やコストの面を考慮すると、大量生産の場合は金型を用いた成形がおすすめです。
2.材料の変更に対応できる
材料となるプラスチックが同程度の収縮率のものであれば、材料の変更があっても一つの金型で対応することができます。
3.設計変更にも対応できる
ベースになる金型が一つあれば、途中で設計変更があった場合も一から作り直す必要はなく、金型を更に削ったり溶接して肉盛りをしたり、「入子」と呼ばれる部品を入れ替えることで形状の変更に対応可能です。
金型設計の基本
樹脂の射出成形を行う際は、成形品の品質や効率に直結する金型の設計が非常に重要です。図面どおりに成形品を完成させるためには。金型を高精度に仕上げなければなりません。また、その材質選びも重要です。設計段階では慎重に検討し、専門知識や経験を活かして最適な金型を設計することが求められます。
まずは、金型設計の基本として特に考慮すべき事項について解説します。
1.どのような射出成形機を使用するのか
使用する射出成形機の種類によって、金型の設計も異なります。安定した製品を作るためには、製品に合わせた適切な射出容量、射出圧力、型締め力などの能力が必要になるため、射出成型機の選定は極めて重要です。成形品のデザインに合わせて射出成形機を選択したうえで、金型を設計しなければなりません。
2.金型の材料の決定
金型は、高温・高圧に耐えられるように金型鋼を使用するのが一般的です。金型の寿命や耐久性を考慮し、適切な金型材料を選択する必要があります。
3.金型の構造
金型は、成形品の形状に合わせた形状と構造が必要です。主な部品としては、ノズルタッチ部、ランナー部、製品部入れ子部、エジェクターピン、ベース、ガイドピン等があります。適切な形状と構造に設計することで、安定した品質の成形品を生産し続けることができます。
4.組み立てと耐久性、メンテナンス性
メンテナンス性を考慮して設計することが重要です。耐久性も考慮して適切な材料と設計を選択することで、製品品質の精度を確保し、金型の寿命を延ばすことができます。
射出成形に使用する金型の種類
射出成形では圧力をかけながら熱した樹脂を流し込むため、金型の耐熱性や耐久性が必要となります。また、部品やパーツなどを量産する場合は金型を何年も使用するため、耐摩耗性も必須です。そのため、金型には合金工具鋼やハイス鋼、超硬合金、セラミックなど、機械性質が優れた金属素材が用いられます。
射出成形金型は、成形品を囲んで凸部と凹部に分割されます。凸部はコア(Core)、凹部をキャビティー(Cavity)と呼び、合わせたときの隙間に溶かしたプラスチック樹脂を射出(充填)します。金型の中で冷やし硬化させ、取り出したものが射出成形製品です。
代表的な金型構造
1.ピンゲート タイプ
<長所>
- 製品とランナーが自動で別れて出てくるため、製品取り出し後にランナーを処理する必要がない。
- サブマリンゲートの様な、ランナーカット時のカスが発生しない。
- ランナー部が製品と別れているため狭い面積に製品をレイアウトできる。
<短所>
- 製品の表面にゲートが凸形状に残る。充填圧力のロスが大きいため外観不良が発生しやすくなり、流動性の悪い材料は不向き。
- 金型構造が複雑になるため、金型費用が高くなる上、金型サイズ(特に厚み)が大きくなる。
2.サブマリンゲート タイプ
<長所>
- 製品とランナーが自動で別れて出てくるため、製品取り出し後にランナーを処理する必要がない。
- 金型がコンパクトで安く作れる。
- ゲート跡が側面に小さく付くが、凸になる事はなく、ピンゲートより目立たない。
- ピンゲートよりランナー重量の軽量化が可能。
<短所>
- 常に金型にランナーが擦れるため削れカスが発生しやすく、外観不良の要因となる。
- 充填圧力のロスが大きいため、外観不良が発生しやすくなる。
- 製品とランナーが同じ所から出るため、分ける必要がある。
3.サイドゲートタイプ
<長所>
- ゲートが大きく作れるため圧力損失が少なく、流動性の悪い材料に向いている。
- 射出ユニットから製品までの距離を短く取れるため、ランナー重量を軽くできる。
- 金型構造がシンプルで、安く早く製作が可能。
<短所>
- 製品とランナーが一体で出てくるため、成形後に切り取る必要がある。
- 射出ユニットから製品までの距離を短く取れる分、ガス抜きを設定できる箇所が限られてしまうため、射出ユニット内で分解したガス等が製品まで辿り着きやすい。
特殊な金型構造
最近の成形品は、コストや外観の改善で複雑な構造、無駄のない生産等の要求が強いため、先程の基本構造を発展させた以下の様な構造が増えています。
ホットランナー構造
<長所>
- 製品だけ出てくるので、ランナーの処理をする必要がなく使用材料も少ない。
- サブマリンと同等のゲート跡しか残らない。
- 直接製品に溶けた材料が注入される為、圧力損出が少なく、充填率が安定する。
<短所>
- ホットランナーユニットが必要なため、金型費や維持費が他の金型と比べて高額。
- 溶けた材料が直接製品に注入される為、材料が分解したガス等の影響を受けやすい。
- 金型構造が複雑になるため、他のランナータイプと比べてメンテナンス性が悪い。
- 設計変更等、後からの対応が難しい。
回転抜き構造
<長所>
- スクリューキャップ、ネジ、ウォーム等のアンダーカット形状を成形できる。
※モーター式回転抜きやメカニカル式回転抜き等、回転させる機構は複数あります。
<短所>
- 機構が複雑になる。
- 回転部分は常に擦り合わさるため、摩耗が激しく、金型の耐久性が低くなる。
スライド構造
<長所>
- 金型開閉方向に対し、製品が抜けてこれない形状(アンダーカット形状)を作る際に、開閉方向に対し垂直方向へ動く機構(スライド)を利用して金型を作る。
※スライドを開く距離(開き量)が大きい製品の場合は、シリンダー等を利用する場合もある。
<短所>
- 入れ子の合わせる箇所が複雑になるためバリや段差等の外観不具合が発生しやすくなる。
- 多数個取の場合、スライド構造の幅を確保するため金型サイズ、ランナーサイズが大きくなる。
日邦産業の強み 〜当社独自のインサート成形技術〜
インサート射出成形とは、金型にあらかじめ金属のネジや端子など(インサート品)を入れ、そのまわりに樹脂(プラスチック)を注入し、一体に成形(複合成形)する技術です。日邦産業は自動車部品をはじめ、電気・電子製品用途でインサート射出成形品を数多く生産しています。
この成形方法により金属と樹脂を複合化させることで、それぞれの材質が持つ特性や機能(金属:高剛性、導電性など/樹脂:軽量、絶縁性など)を同時に利用できることと、金属単体では実現できない形状を樹脂と複合化することで実現させることができる等のメリットがあります。
<事例1・弊社開発技術>封止インサート技術(金属⇔樹脂 シール(密着)技術)
インサート射出成形を行う場合、二つの素材の間には接合界面が存在するため、その接合力や気密性が課題となります。この問題点を解消するため、当社はインサート射出成形において金属と樹脂の接合界面に接合力や気密性、親和性を付与する技術を採用しています。
1次シール材成形として、金属インサート部品の密着性に適した樹脂をアウトサート成形し、そのインサート部品を2次インサート成形することで密着性を高めることが可能となります。
シール材成形
2次インサート成形
一般的に樹脂と金属の界面は密着しておらずシール性は確保できていないため、電気的絶縁や部材腐食の要因となることが多いです。このような当社の独自の工法であれば高度なシール性が確保でき、熱応力に対しても有効です。
<事例2・弊社生産技術>割れないマグネットのインサート成形品
近年、高度化する技術の中でマグネットの磁力(ヒステリシス曲線)を利用した、より「軽量」で「精密」なセンサー部分の要求が増えており、そのためにマグネット部分のインサート成形は不可欠となっています。
センサー部分に利用されるマグネットは、少しの衝撃でも割れやすく、通常のインサート成形時の樹脂圧(約500kg/㎠〜800kg/㎠)に耐えきれない場合が多いため、割れやクラック等の不良が発生してしまい、高い不良率で量産を行うことが常識となっていました。
弊社では、そのマグネット部分のインサート成形に使用する金型と成形機を利用してマグネットにかかる圧力のバランスを制御する事で、割れを抑制して高い良品率の量産を可能とし、マグネット部分のインサート成形品の「低価格化」を実現しました。
※インサートされるマグネットの材質、肉厚、内・外径、高さ寸法等で対応方法が異なりますので、詳細については別途お問い合わせください。
ダイカスト鋳造製品の試作や小中ロットの生産をご検討の加工メーカー様へ
当社では、石膏型を使用した鋳造により、金型コストを抑えた短納期の試作をご提案可能です。
「精密石膏鋳造」のご紹介はこちら射出成形に関するお問い合わせ・試作のご依頼はこちら
お客様のご要望に合わせた構造・機構設計を承ります。必要なサイズ、機能、特性などの情報を基に、最適な設計仕様をご提案させていただきます。
日邦産業株式会社お問い合わせフォーム
国内3拠点に加え、アセアン(タイ・マレーシア・ベトナム・インドネシア・フィリピン)に生産拠点を構え、グループ内で展開されたモノづくりノウハウにより、高品質な製品をご提供しております。